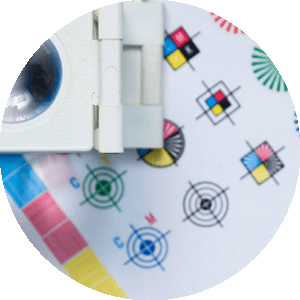
Prepped for Print: What to Consider When Packaging Design Files for Production
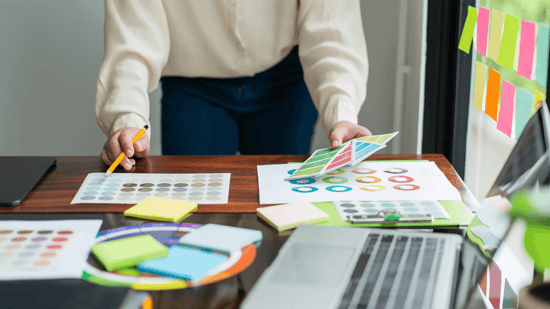
There are many decisions designers need to make in order to get the most out of digital inkjet print, from the right substrate to print on to choosing the ideal color space for your inkjet device. Packaging design files for production is a whole separate beast in terms of facilitating a smooth, error-free print process.
“Delivering all the packaged elements properly can eliminate confusion and wasted time for you as well as your print provider,” write Elizabeth Gooding and Mary Schilling, authors of The Designer’s Guide to Inkjet, 3rd Edition. “When your print provider doesn’t need to rework your files, hunt for missing fonts, or clarify finishing instructions, you’re more likely to achieve your deadlines and avoid extra support costs.”
With this in mind, let’s look at a couple of key things to consider when packaging design files for production to help maximize the potential of printing on digital inkjet.

Why is proper design file packaging important?
Aside from establishing and maintaining a productive, collaborative relationship with your print provider, proper design file packaging has a number of real-world implications, especially in terms of saving time and money.
When your print partner receives a file that conforms to their specifications, processes, and understanding of customer requirements, the printer has everything they need to produce your design with the kind of stunning color and print quality digital inkjet provides. Design files that contain missing elements or that don’t conform to specifications can result in costly production delays, or, worse, a final product that doesn’t accurately reflect your design.
“The fact is file inefficiency hit their bottom line,” write Gooding and Schilling. “When the files a print provider receives need work, it costs them money that isn’t often directly charged to the customer who caused the problem. When files slow the printer down or cause delays at the start of the job, it eats away at their profitability.”
Some of the key components that can affect the efficiency of your finished file include:
-
Providing images in the proper resolution
-
Selecting the right document color space
-
Assigning CMYK color values from a printed image using correct paper, ink, and output profile
-
Preparing static and variable images
-
Selecting an appropriate image file format and compression setting
-
Saving to the correct PDF settings
Why considering fonts is key when packaging design files for production
Ensuring that complete font sets are available for every single font size used in your design is critical to creating delay-free inkjet print. Often fonts are loaded in as restricted, meaning that they only embed the actual characters used in the PDF file.
“If you marry the PDF with the text from an external data source, you could call for characters that were not used, and therefore embedded, in the PDF template,” explain Gooding and Schilling. “If those characters are not part of the embedded fonts, your job will fail in production — or worse, run the whole job with missing letters.
Printers sometimes ask for fonts to be outlined before saving to avoid font compatibility issues. For example, if a document includes variable data, never outline the font for readable text within the document. This rule also holds true for static documents that are text-heavy. Rendering images from the actual font will provide better print clarity, with the only exception being large text elements that are used as graphics.
Why accounting for colors is key when packaging design files for production
Perhaps the most important aspect of accounting for colors when packaging design files for production is aligning any color correction and setting CMYK color values to the entire workflow. Many color composition tools have a setting that tells them whether to use the color definitions from the input file or to override them with the software’s own color management settings.
This is where Gooding and Schilling urge a clear line of communication with your print partner to make sure the appropriate color settings are applied before production begins.
“If you actually want to use the settings you so carefully specified, make sure this is clear to your print provider.”
Why a soft proof is important when packaging design files for production
Requesting a soft proof from your print provider can help verify that variable data has been applied. This test file usually comes as a PDF generated from the composition software using the PDF you generated from your design software as input, along with a variable data test file.
“While the soft proof may not be an exact match for the press output, the color should be consistent,” write Gooding and Schilling. “It should also surface any layout issues from fitting variable content.”
Using Adobe Acrobat Reader® to compare the two soft proofs — your original and the PDF created by the composition tool — can help you spot differences between the two, and this can also help determine if your settings have been carried through the composition portion of the workflow.

These aspects of packaging design files for production will help you avoid errors or defects when printing on digital inkjet, but there’s so much more to know about how to ensure you’re getting the most out of printing on an inkjet device. Download The Designer’s Guide to Inkjet, 3rd Edition to learn more.
See More Like This
See More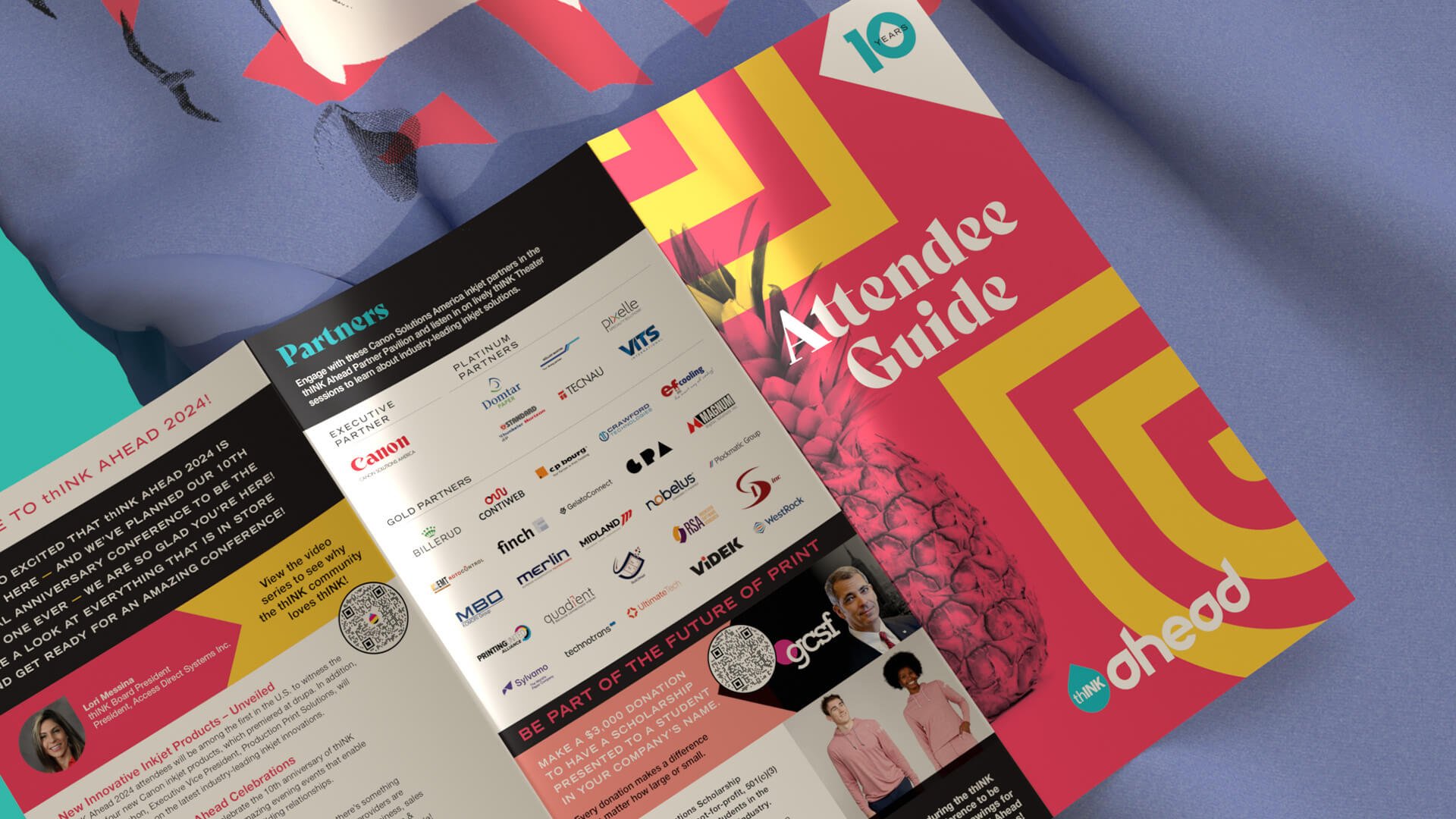
Marketing Collateral
Project Spotlight: Gloss-Coated thINK Ahead 2024 Attendee Guide Trifold
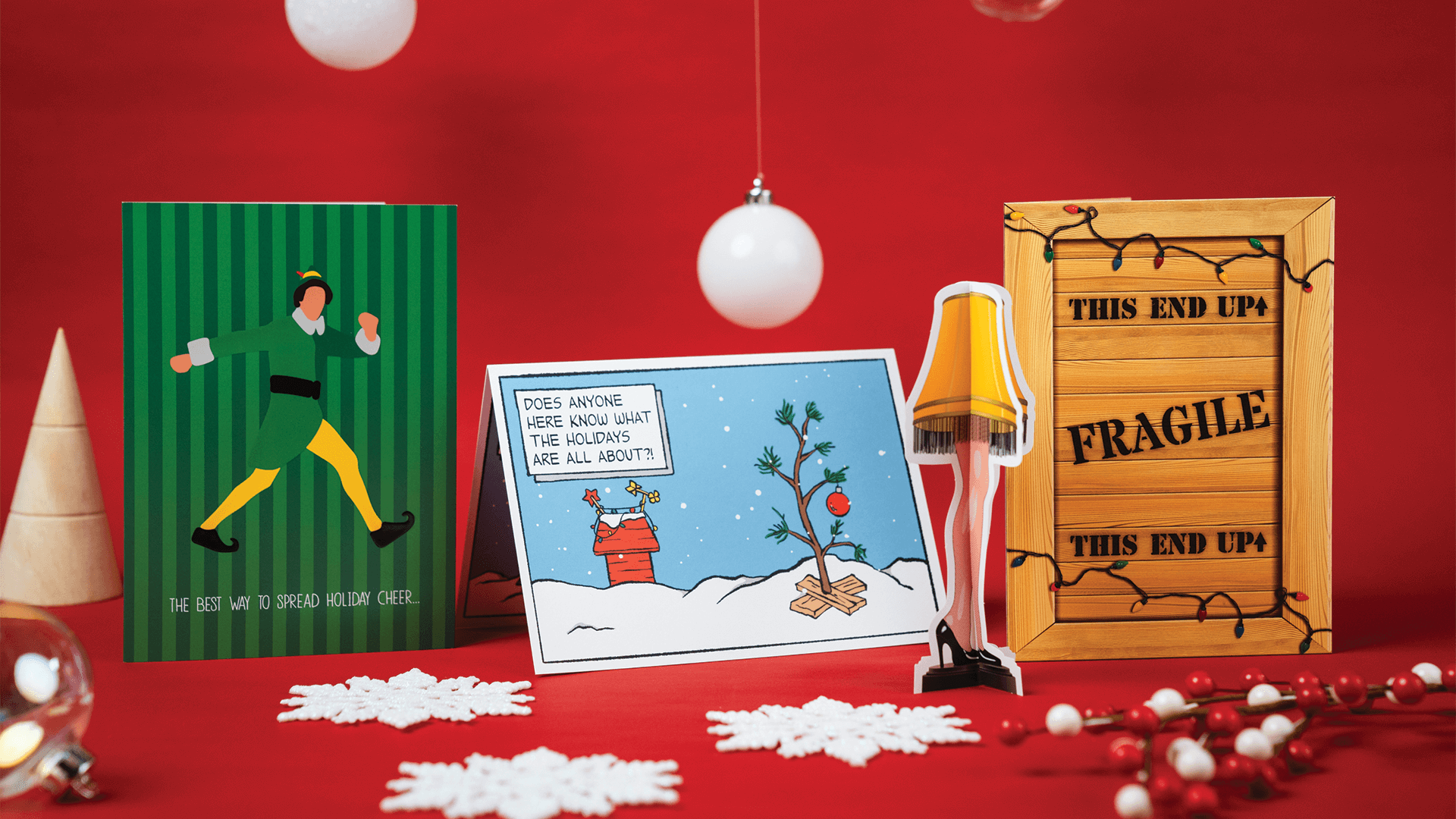
Marketing Collateral
Project Spotlight: How These Movies Inspired Interactive Holiday Greetings
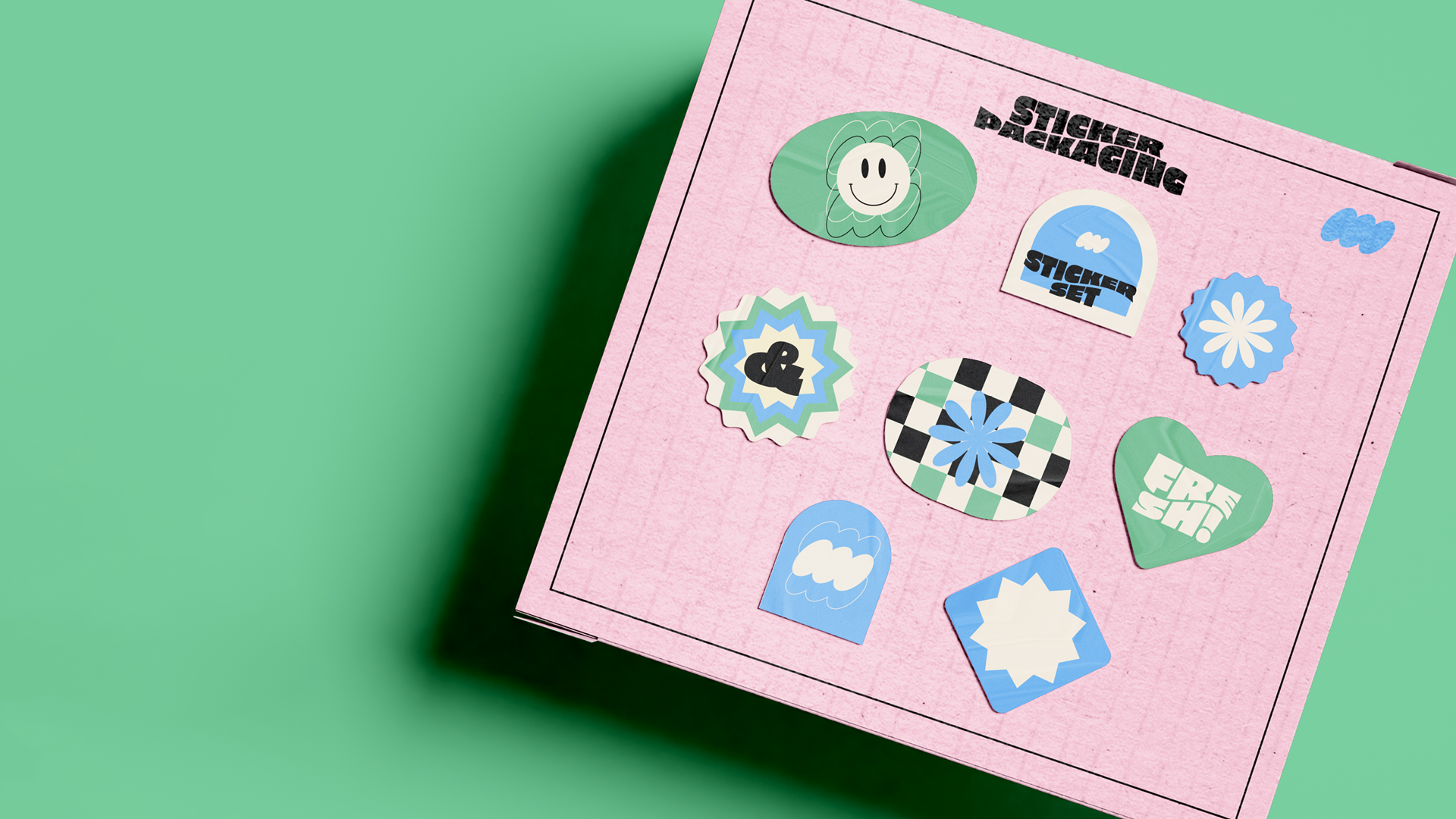
Marketing Collateral
LEARN: 4 Tips for Designing and Printing Stickers
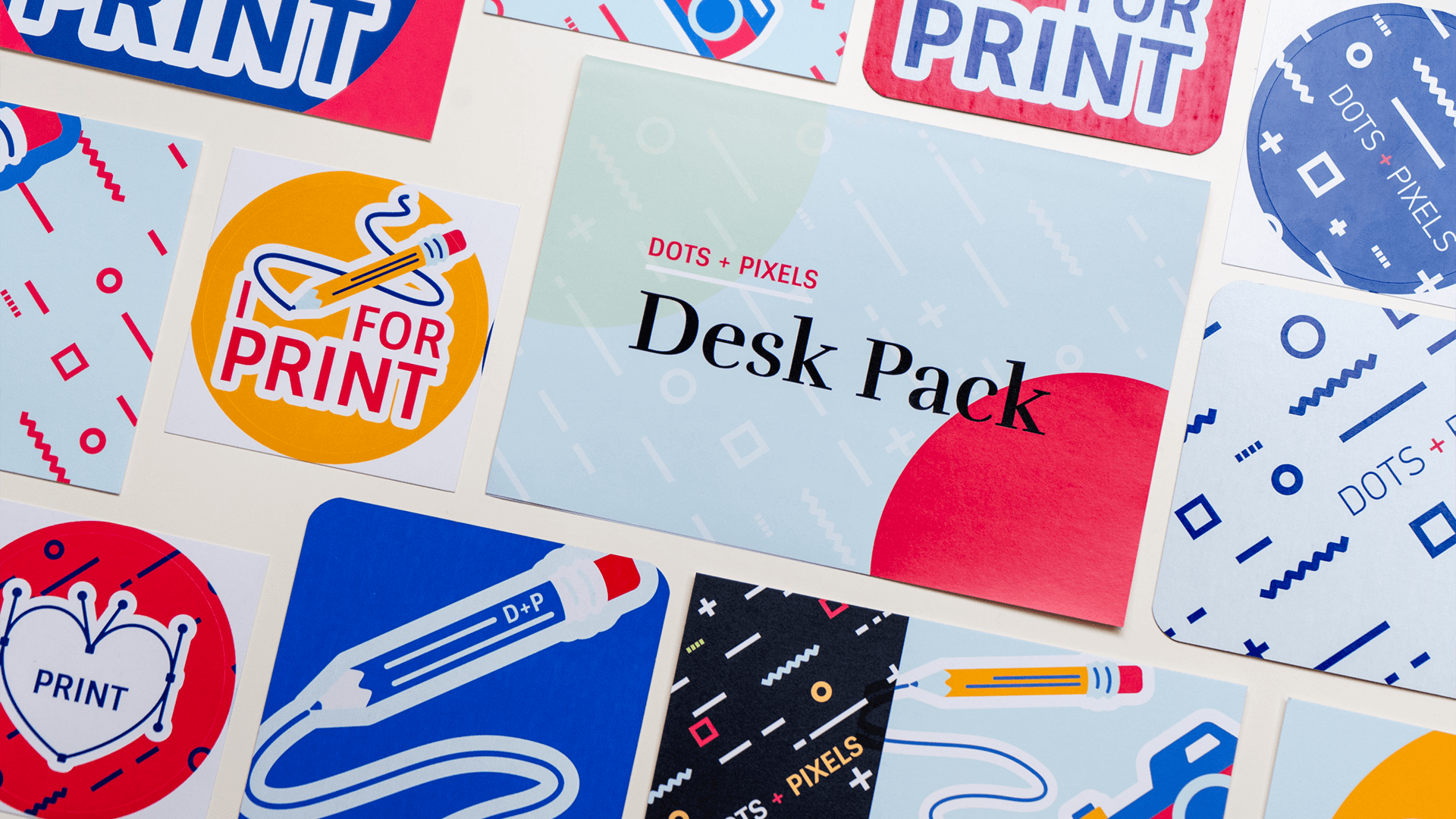
Marketing Collateral
Project Spotlight: A Swag Pack that Rewards and Inspires