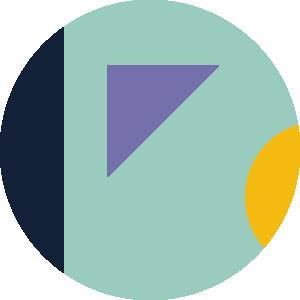
How to Avoid Oversaturation When Designing with Large Blocks of Color
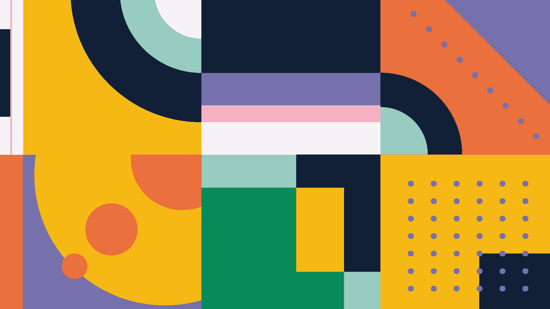
Vibrant blocks of color can help designers direct the attention of their audience and inject a design project with a little extra dramatic effect. But large blocks of color also require more ink, and, if the coverage becomes too great, these blocks can oversaturate the substrate. This can not only lead to blurry or muddled swatches of color, but it can also create issues with finishings down the road.
“We aren’t just talking about how many square inches (or centimeters) have ink on them, but about the amount of ink on any particular square inch or across any part of the sheet,” write Elizabeth Gooding and Mary Schilling, authors of The Designer’s Guide to Inkjet, 3rd Edition. “Any spot on the sheet that becomes sodden with too much ink may cause paper deformities.”
The ability to get the most out of digital inkjet depends on the kind of paper designers choose, and the ability to create design files with said paper in mind to streamline or troubleshoot the design process. Avoiding oversaturation with large blocks of color is no different. Here, we’ll look at a couple of things to consider in terms of the paper qualities necessary to avoid oversaturation when designing for digital inkjet.

Be mindful of basis weights
The choice of basis weight will impact the level of ink coverage a design can support. This choice is complicated by the fact that the basis weight that’s most appropriate for a particular amount of ink coverage will differ based on the porosity of the paper — we’ll discuss this more in a moment.
“Porous offset papers lighter than 90 gsm may not be able to handle even a 240-percent maximum coverage,” write Gooding and Schilling. “Heavier and thicker papers that are inkjet treated or inkjet coated may be able to handle a slightly higher TAC.”
Papers of 90 gsm and lower tend to curl toward whichever side has heavier ink coverage — if coverage is heavier on one side of the sheet — so designers should specify sheets of more than 90 gsm to prevent curling or other types of defects.
Total Area Cover (TAC) refers to the total amount of ink that can be in any one area of the sheet — TAC describes the highest total thickness of combined ink for a job. TAC is vital relative to a paper’s basis weight because it helps designers know how much ink saturation a sheet can take before oversaturation takes place.
“TAC is generally referred to as a percentage, such as 200 or 240, based on combining the total percentage of C, M, Y, and K required in a design document,” explain Gooding and Schilling.
Accounting for basis weight — combined with TAC — will help ensure your design files produce the kind of exceptional color quality digital inkjet can provide without incurring print defects as a result of using too much ink.
Prioritize the porosity of your paper
While specifying the right basis weight can help avoid oversaturation when designing large blocks of color, specifying the type of paper — uncoated, coated, and inkjet treated or inkjet coated — can play just as big a role in avoiding unsightly oversaturation. This is due to the porosity of each sheet, or how much ink is actually absorbed into the fibers of the paper — the greater the absorption, the more likely it is for oversaturation to take place, and the more careful designers must be.
Uncoated paper lacks any kind of coat or seal on the fibers of the paper, making it much more porous and more susceptible to large amounts of ink absorption. As such, this makes designing large blocks of color on uncoated sheets more tricky given the increased likelihood for colors to become muddled or blurry.
Coated papers are better able to resist high levels of ink absorption as the specialty coatings make them less porous.
The choice between inkjet coated and inkjet treated sheets can also play a role in avoiding oversaturation. Inkjet coated sheets come in a variety of surface finishes from very shiny (gloss) to less shiny (matte). The surface of inkjet coated stocks dries very quickly, which helps create a broader range of colors compared to uncoated sheets.
Inkjet treated paper uses a treatment that blankets and seals the wood fibers. These treatments separate the colorants from their carrier liquids, which better allows the colorant to remain on the surface of the sheet and thus creates better print and image quality. Inkjet treated sheets also have a reduced porosity to prevent the ink from absorbing into the sheet along with the carrier liquid.

While accounting for the basis weight and porosity of your paper can help create high-quality inkjet print that is free of production defects, it’s really just the beginning of what you need to know about the choices and techniques necessary to avoid blemishes like oversaturation. The Designer’s Guide to Inkjet, 3rd Edition has everything you need to know to keep oversaturation at bay, and ensure a smooth, streamlined digital inkjet experience, from design to delivery. Download The Designer’s Guide to Inkjet, 3rd Edition to learn more.
See More Like This
See More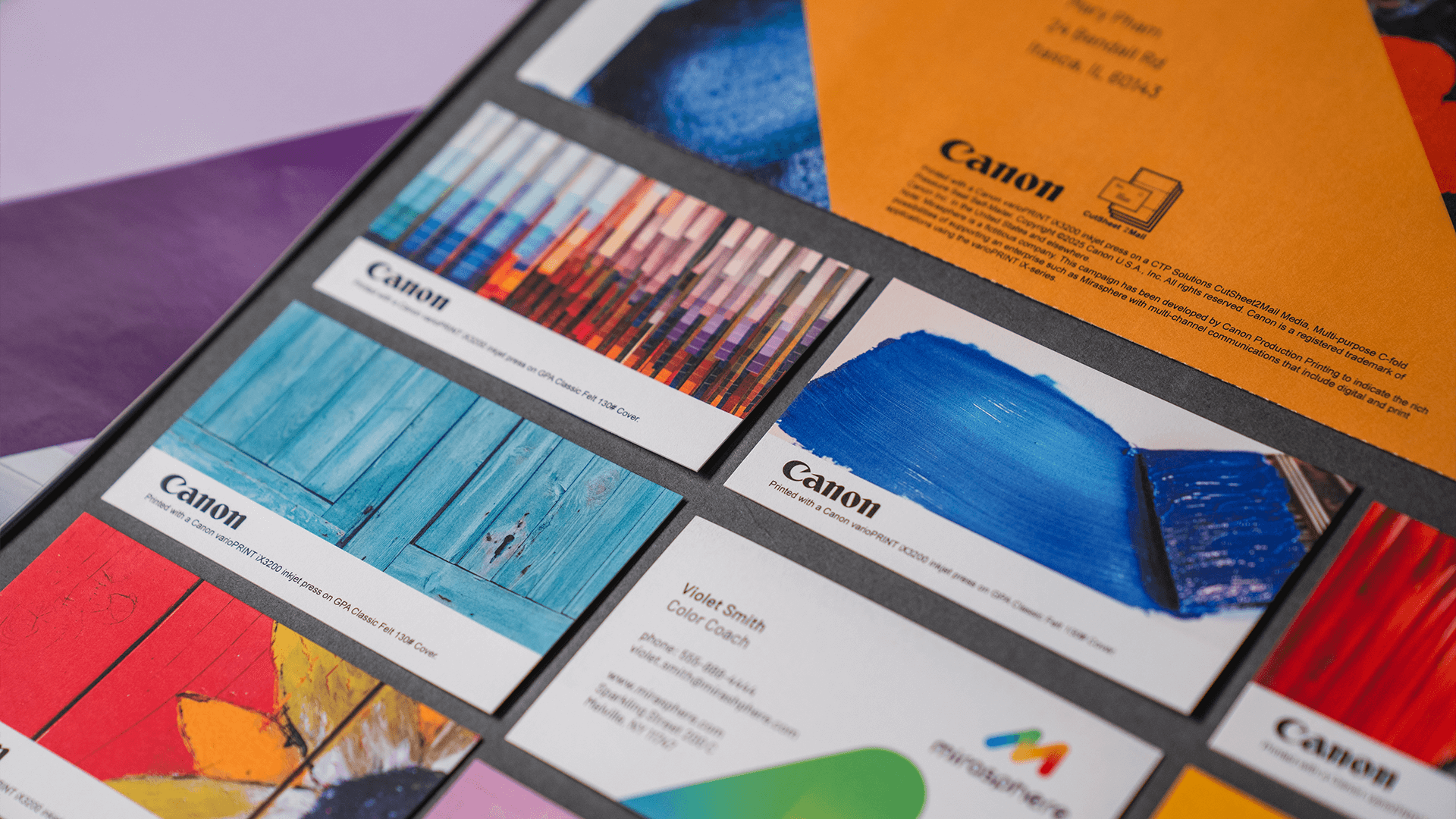
Marketing Collateral
Project Spotlight: A Sample Omnichannel Marketing Package
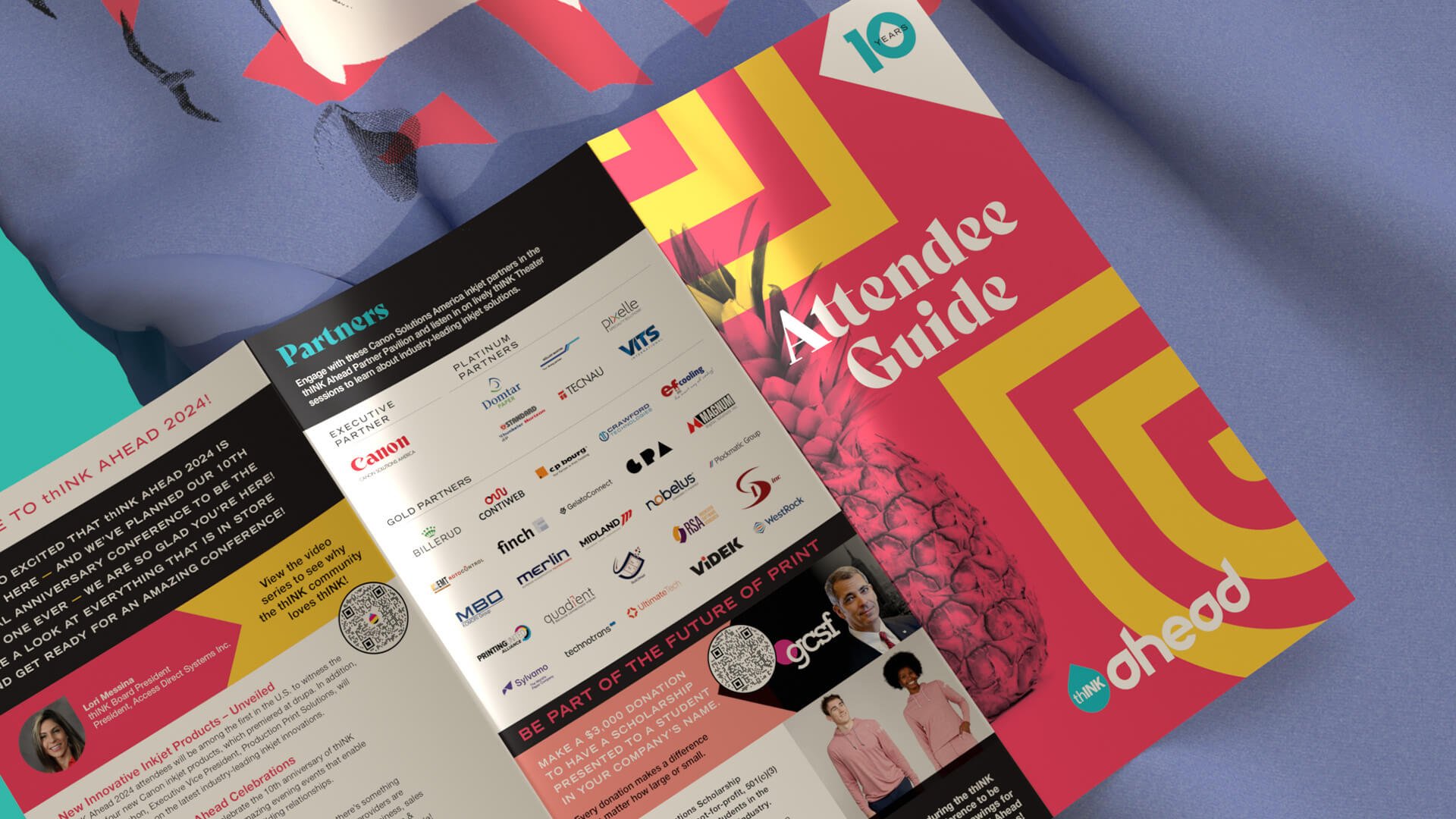
Marketing Collateral
Project Spotlight: Gloss-Coated thINK Ahead 2024 Attendee Guide Trifold
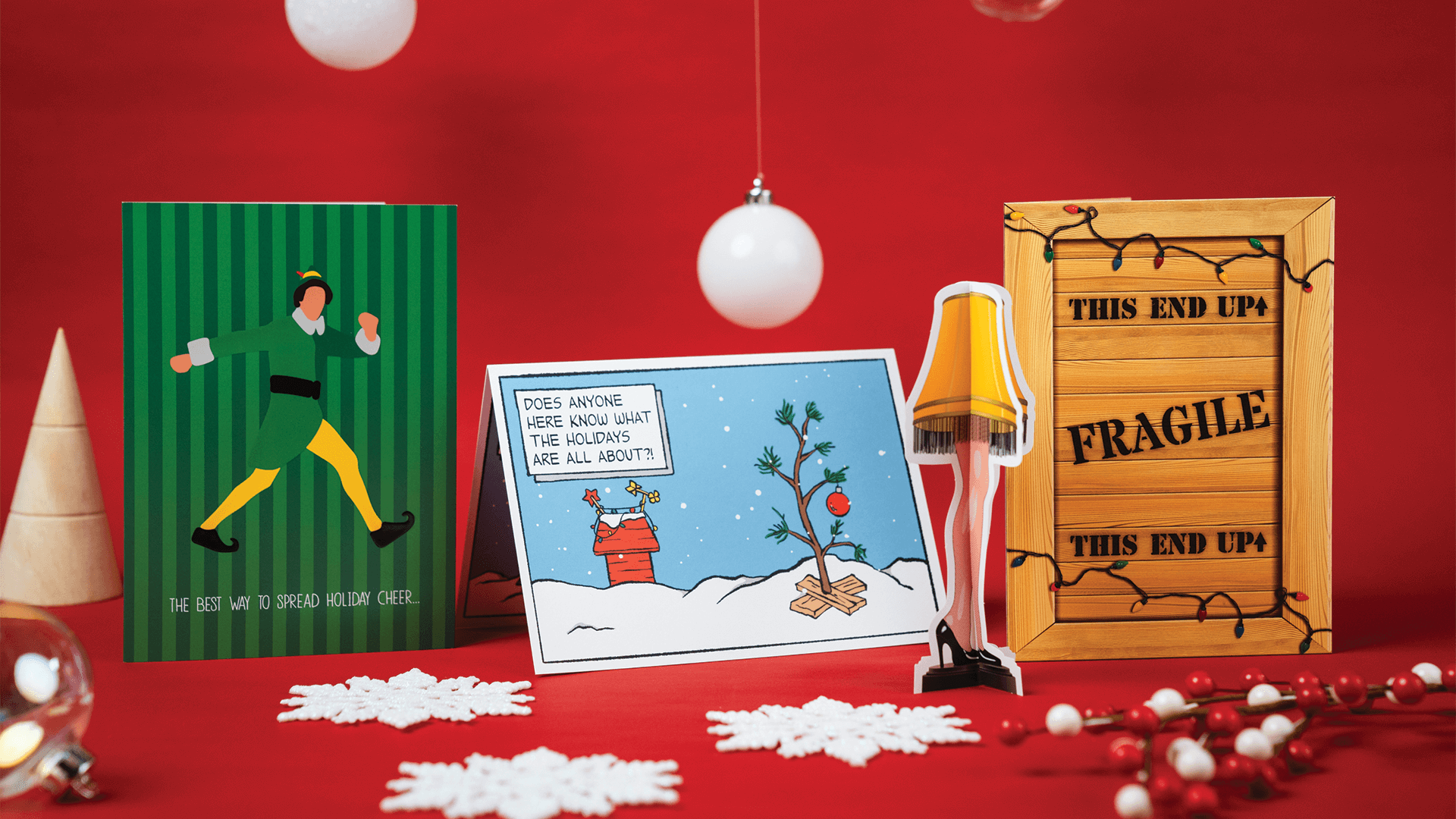
Marketing Collateral
Project Spotlight: How These Movies Inspired Interactive Holiday Greetings
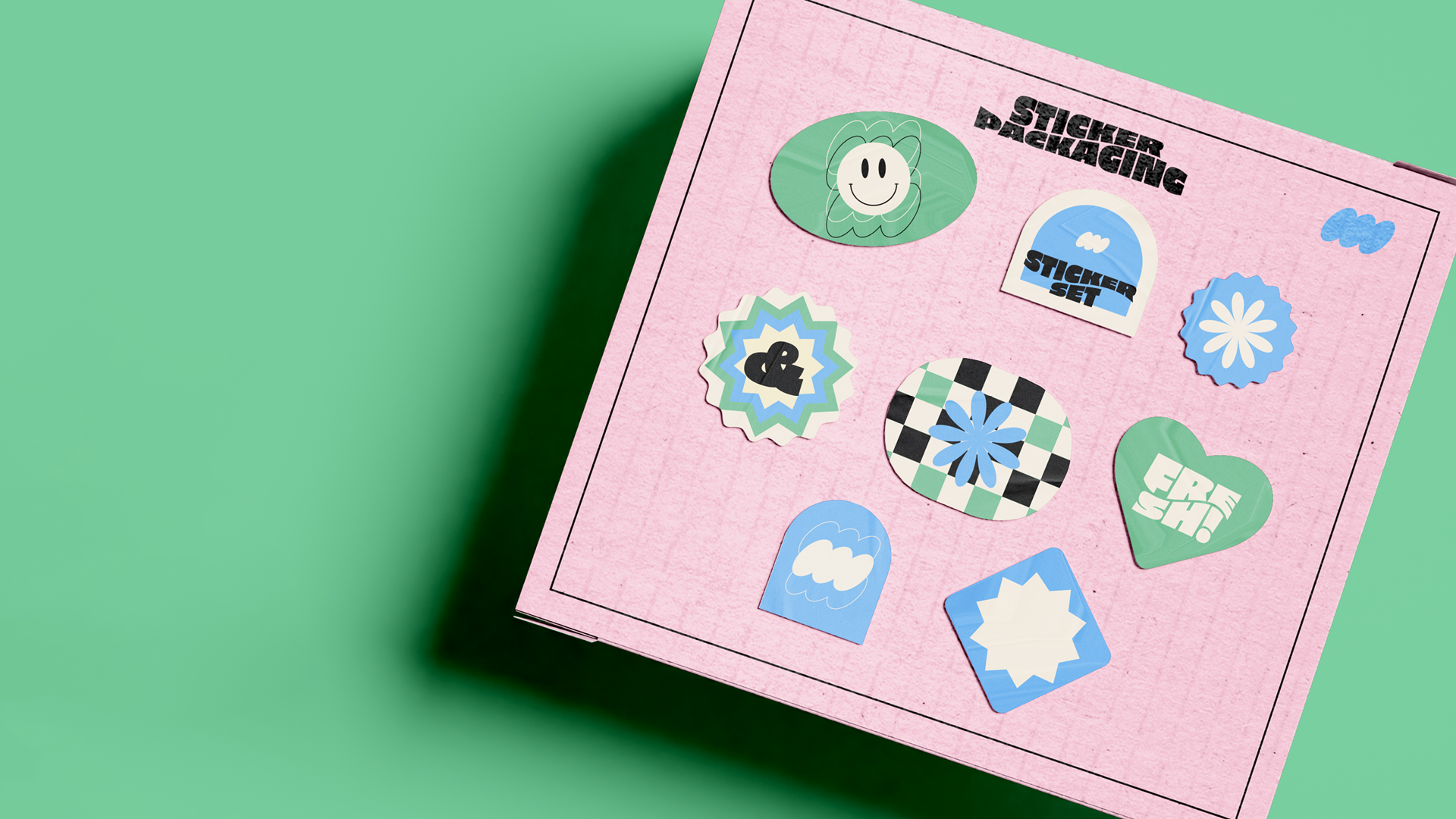
Marketing Collateral
LEARN: 4 Tips for Designing and Printing Stickers